Aktuelle News
- Die sieben Arten der Verschwendung – Lean Management in Produktion und Verwaltung
- Unser europäisches Controlling Verständnis ist weltweit gefragt
- Integrierte Planung – Ein Schlüssel zur verbesserten Unternehmenssteuerung
- 24 Monate Blick nach vorn – Liquiditätsplanung unter dem Blickwinkel des § 18 InsO
Seminarangebot zu diesem Thema
Akzeptanz schaffen in der Produktion für kleinere Losgrößen als Teil von Lean Management?
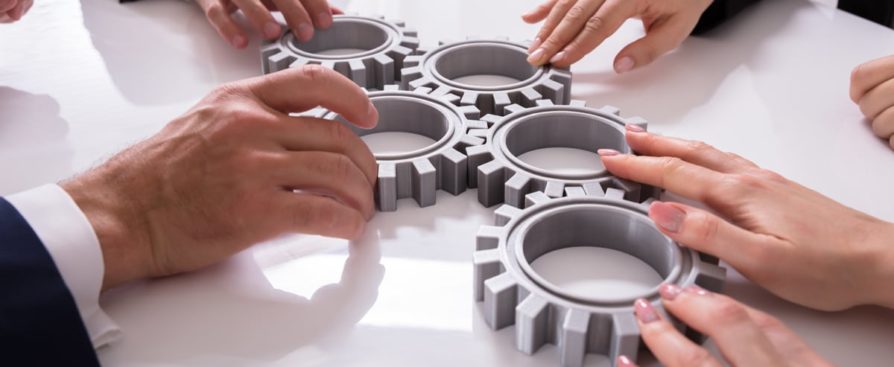
Lean Management ist aktueller denn je! Ob Working Capital Management, Industrie 4.0, Fixkostencontrolling oder die Anpassung der Controlling-Prozesse an die Herausforderungen der heutigen Zeit – am Ende geht es um die Optimierung und Verschlankung von Prozessen. Und das birgt Spannungen für die Organisation, die gelöst werden müssen.
Ein typisches Beispiel aus dem Unternehmensalltag zwischen Controlling, Produktion und Kundenservice ist das Spannungsdreieck zwischen kleinen Lagerbeständen, kurzen Lieferzeiten und zugleich der Reduktion der Stückkosten in der Fertigung.
Das Lean Management setzt zur Lösung des Spannungsdreiecks auf die Verkleinerung der Losgrößen. Dadurch steigen aber die relativen Rüstkosten. Als Gegenmaßnahme setzt Lean Management auf die Verschlankung der Prozesse für schnelle Loswechsel. Diese Maßnahmenkombination ist vordergründig kontra-intuitiv. Sie führt daher regelmäßig zum Streit innerhalb der Produktion und besonders an den Schnittstellen zu Arbeitsplanung, Controlling und Kundenservice. Dieser Streit behindert im Unternehmensalltag die Umsetzung.
Die Fragestellung lautet daher, wie kommuniziert man die Notwendigkeit und den Vorteil kleiner Losgrößen in der Produktion, um dort mehr Akzeptanz zu schaffen, die wiederum notwendig ist, für die Umsetzung der Optimierungsmaßnahmen.
In einem Fallbeispiel beschreibt Dr. Christian Artmann eine aktuelle Aufgabenstellung und die dazu möglichen kommunikativen Maßnahmen und Inhalte.
Ausgangslage:
Im Rahmen der Umsetzung von Lean Production wurde bei einem Pumpenhersteller die Reduktion der Losgrößen als Maßnahme festgelegt. Damit stiegen die relativen Rüstzeiten deutlich an. Die Fertigungsplanung selbst erfolgte parametrisiert durch ein PPS System. Im Rahmen der Planung und Umsetzung der Gegenmaßnahmen zur Optimierung der Rüstzeiten wurde seitens der Belegschaft immer wieder die Sinnhaftigkeit kleiner Losgrößen bezweifelt. In der Folge wurden die Optimierungen nur mit halber Kraft vorangetrieben.
Problem:
Für die Belegschaft ist der Sinn kleiner Losgrößen schwer nachvollziehbar. Auf der einen Seite werden die Losgrößen scheinbar zu klein und damit unproduktiv gewählt und auf der anderen Seite wird viel Aufwand getrieben, die Rüstzeiten pro Los zu senken. An diesem Punkt ist die Kommunikation mit dem Betriebsrat und der Belegschaft entscheidend.
Sieben spezifische Ursachen für kleine Losgrößen
- Kunde bestellt unregelmäßig. Daher würde das Zusammenlegen entweder lange Lieferzeit für den Kunden oder ein hohes Risiko für die Produktion bedeuten, teureres Lager aufzubauen (Kapitalbindung, Platz, Materialbewegung, Schaden- und Obsolet Risiko).
- Bewusste Splittung von Aufträgen, um nachfolgende Engpassmaschinen und Prozesse nicht zu überlasten. Die Zusammenlegung der Lose mit nachfolgender hoher Engpassbelegung würde zu verspäteter Lieferung anderer Aufträge führen.
- Ausschuss in einem späteren Fertigungsschritt, bis hin in die Endkontrolle, der zur Wiederauflage des Auftrags oder von Teilen des Auftrags als kleines Los führt.
- Bewusste Splittung von Aufträgen in kleinere Lose, da nachfolgendes Material nicht für alle Teile des Auftrags verfügbar ist. Ohne Splittung des Auftrags in kleine Lose würden einzelne Teile des Auftrags an verschiedenen Schritten der Fertigung stehen bleiben und eine unübersichtliche Lager- und Fertigungssituation auslösen (Siehe auch Anmerkungen unter 1).
- Eiliges Ersatzteil, das für den Kunden wichtig, zur (Wieder-) Inbetriebnahme wichtig ist oder zur Erfüllung unserer Service-Zusagen wichtig ist.
- Es fällt ungeplant und kurzfristig eine Ressource aus. Es kommt zum Rückstau in der Fertigung. Auf den Rückstau werden dann neue Aufträge und bestehende Aufträge nicht auf einmal wieder in die Fertigung gegeben (Blockade von Engpassmaschinen). Stattdessen werden die Aufträge nach Dringlichkeit, Engpassmaschinen, Materialverfügbarkeit, Teilbarkeit, etc. in Lose zerlegt und nach und nach die Fertigung wieder eingeschwungen.
- Planungsfehler vom System oder von den Planern, z.B. Tippfehler, logische Fehler, Programmfehler, etc. die systemisch behoben werden müssen.
Lösung:
Nach heftigen Diskussionen wurde folgendes Vorgehen abgestimmt:
- Praxisnahe Definition von sieben spezifischen Ursachen für kleine Losgrößen, um jeder Losgröße eine nachvollziehbare Begründung zu geben.
- Auszählen der Losgrößen nach den sieben Ursachen und Visualisierung.
- Regelmäßige Betrachtung der Auszählung im Rahmen des Shopfloor Managements.
Ergebnis:
Auf Auszählung der Begründung der Losgrößen, der Visualisierungen und der Besprechungen mit der Belegschaft konnte die Einsicht für die Notwendigkeit kleinerer Losgrößen deutlich erhöht werden. Damit konnten dann die wichtigen Einzel-Maßnahmen zur Rüstzeitreduktion im Konsens mit allen Beteiligten auf den Weg gebracht werden.
Fazit:
Veränderungen im Unternehmensumfeld bedeuten, dass neben den prozessualen Maßnahmen immer auch kommunikative Maßnahmen zu berücksichtigen sind. Die am Prozess Beteiligten müssen von der Notwendigkeit der Veränderung überzeugt sein oder diese zumindest nachvollziehen können. Dies führt zu besseren Ergebnissen aus der Umsetzung der Maßnahmen.